Firing Pottery
Firing pottery is both exciting and challenging. Perfect your
clay pot projects
through firing. Follow the process here from throwing
ceramic greenware pots to
painting clay pots with glaze.
Lifecycle of a Pot
When the life of a clay pot begins, it's just a ball of clay in your hands. With a little practice, elbow grease, and mud, it becomes a pot. Until the pot is fired, it is called
ceramic greenware.
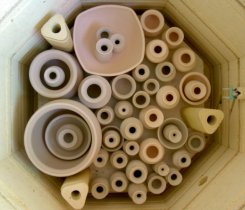
Electric ceramics kiln
being loaded with ceramic greenware.
Your greenware pot is then fired slowly to bake all of the moisture out of the clay. This first partial firing or
bisque ceramics firing
hardens the greenware so it can be handled without breaking. After the pot has been fired once it is called bisque or bisque ceramics.
Finally, your bisque is dipped, sprayed, or painted with
pottery glazes
. Once the glaze dries, it is fired a second time to a much hotter temperature. This is called the glaze firing.
At this point the clay particles fuse together or "vitrify", and the pot is "mature". Mature clay is highly water resistant and durable.
Note: Low fire pottery is less water resistant and durable than high fire pottery due to the additives that are required to help the clay to fuse at such low temperatures.
In this final firing the glaze also vitrifies and fuses to the clay. The glaze further increases the water resistance and durability of your clay pot project. When this firing is finished your pot is complete!
Learn more about how to fire an electric ceramic kiln.
Right: Electric ceramic kiln being loaded with glazed pottery.
Kiln Types
There are three major kiln types. Click on one of the links to learn more about each type.
Wood Fired Pottery
Gas Pottery Kiln
Electric Ceramics Kiln
Alternative Firing Methods
There are a number of alternative firing methods as well including: saggar, barrel, pit and
Raku firing.
Many of these firing methods are not only the simplest, but are also the oldest methods of firing. Pit firing consists of burying the pottery and then creating a fire on top of the pots.
Raku firing involves taking red hot pottery out of a gas kiln and placing into combustible material. This causes carbon to adhere to the glaze surface creating really fun glaze effects.
Firing
Firing pottery- is the process of controlling the heat rise in the kiln to produce the desired results. This accomplishes two things for the pots.
First, it heats the pottery just to the point of maturity, bringing out it's highest quality and function. Second, it allows the potter to manipulate the fuels to create special glaze and surface effects.
When firing pottery, there are several ways to determine when the pottery has reached the maturation point. The most common and reliable method is with
pyrometric cones.
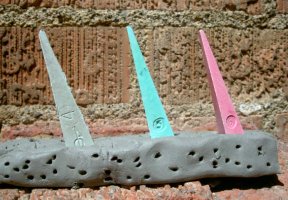
Pyrometric cones
are specially formulated cones of clay material designed to melt after they have experienced a certain amount of "heat work".
Heat work- is a combination of temperature and time.
Therefore, a cone fired over a longer time can melt at a lower temperature than a cone fired over a shorter time. This gives the potter a very accurate gauge of how the firing is going.
Many kilns also contain pyrometers which measure the actual temperature in the kiln. This provides a rough estimate of how the firing is progressing.
Finally, many potters have an eye for gauging the temperature in the kiln by the color of the glow on the pots. By looking into the kiln through a peephole you can see different hews of orange, which indicate different temperatures.
Tip: When firing pottery, always follow the kiln manufacturers safety recommendations. Use proper eye protection when looking into the kiln as the light can be damaging to the eye.
If I could recommend only one book about firing an electric kiln it would be Electric Kiln Ceramics: A Guide to Clays and Glazes
by Richard Zakin.
It is one of those beautiful, valuable resources the pages of which have become speckled with glaze, creased, marked, and muddied from loving use.
Almost all of what I understand about firing started from this book.
Some people may find the price prohibitive, but the information in the book is well presented and worth every penny.
I have looked for an acceptable alternative with no luck. If anyone is aware of a better book for a better price, please let me know.
Thanks for reading about the various methods of firing pottery, and Happy Potting.
Return From Firing Pottery
To Pottery on the Wheel Home
Enjoy this page? Please pay it forward. Here's how...
Would you prefer to share this page with others by linking to it?
- Click on the HTML link code below.
- Copy and paste it, adding a note of your own, into your blog, a Web page, forums, a blog comment,
your Facebook account, or anywhere that someone would find this page valuable.